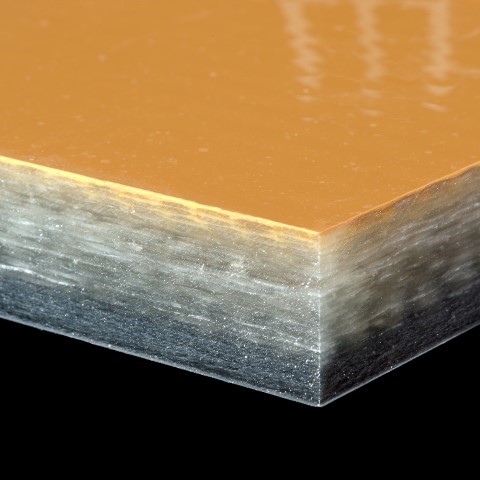
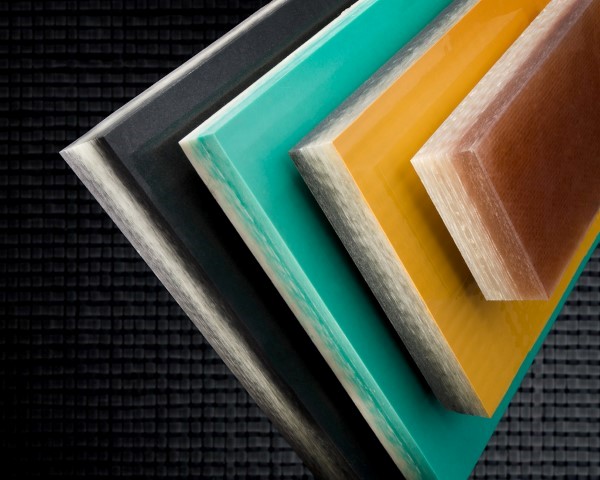
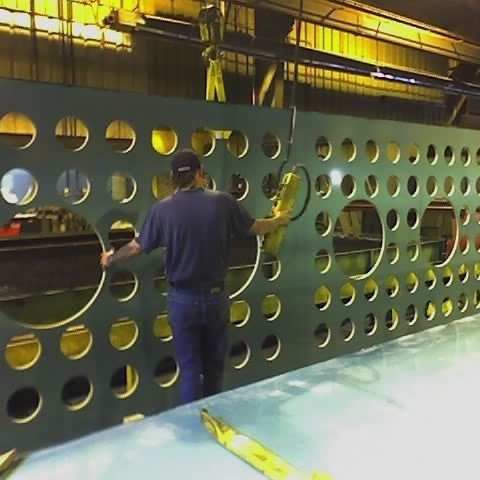
Corrosion Resistant Applications
Fiberglass Reinforced Plastic (FRP) has been used for industrial applications since the 1960's. Adapted from the marine industry, FRP was first used for seawater and other corrosive applications like those found in the pulp & paper industry. FRP is a mature material used in construction with many documented successful case histories. Where metals reach their limits for chemical resistance, maintenance, or for economic reasons, FRP should be your first choice in corrosive environments. FRP panels are lightweight, corrosion-resistant, and above all, virtually maintenance free.
You will find solid fiberglass composite panels in almost any extreme & harsh environment.
FRP Applications
- Commercial, industrial & wastewater
- Fluid containment
- Stack floors
- Chimney liners
- Flue gas desulfurization FDG) units
- Breeching & outlet duct systems
- Mineral processing
- Tanks, vessels & scrubbers
Utilizing specialty formulated resins, Fiber-Tech's solid panels provide industry with a fiberglass alternative to expensive and exotic metals. Chemical additives can be used in the resin system to provide abrasion resistance and/or fire resistance. A combination of E-glass, E-CR glass and C-glass can be used to provide a structural panel with excellent corrosive resistant properties for most any environment. Carbon veils and other additives can also be used to reduce/manage static electricity and abrasion. Fiber-Tech's ability to produce large panels allows the contractor to reduce labor costs by reducing the quantity of field joints/seams.
Fiber-Tech’s FRP is highly resistance to most of the chemicals used today and will not crack, chip, peel, rust, rot or decay. FRP is pound for pound stronger than steel. Fiberglass composite panels strengths make it a preferred choice for demanding industries.
Corrosion Resistant FRP Panels for the Power Industry
The corrosion resistance and physical strength characteristics of Fiber-Tech’s FRP panels lend themselves to many applications in the power industry. Flue gas desulphurization scrubbers,
absorption towers, breachings, stack liners, cooling water transmission/distribution and waste water containment are but a few of the proven power plant applications.
Duct Systems
Duct Systems and breachings of virtually any size have been designed to utilize Fiber-Tech’s flat panels and compliment other components of a fiberglass composites system. Like most other composite FRP structures, these components require little maintenance and never need painting, lowering lifetime cost of ownership.
Other Industries Served
- Chemical processing
- Power
- Pulp and paper
- Waste water treatment
- Mining, smelting and mineral processing
- Petrochemical
Performance Criteria:
Corrosion Resistance:
This is controlled by the laminate structure and the resins used. A wide variety of thermoset
resins are available to meet a wide range of service requirements, such as specific chemical exposure, temperatures, elongation, fire resistance and strength requirements. Many of Fiber-Tech’s panels utilize the physical properties of Ashland's Hetron and Derakane fiberglass resins in order to provide our customers with products which have unique advantages over other conventional materials.
Flame and Smoke:
With the use of additives to the resin system, Class 1 fire rating can be achieved.
Abrasion Resistance:
Additives can be blended into the resin system to achieve an abrasion resistant laminate and surface.
Conductivity:
Depending on your specific panel application, static electricity can be managed through the use of carbon veils and/or special additives in the resin and lamination schedule.
Fiberglass Reinforcements:
The laminate schedule of fiberglass reinforcements can include carbon veils, e-glass woven roving, and chopped strand mats. Glass to resin ratio can be matched to meet job specific criteria specified by your engineering team.
External Weathering Surface:
To improve weathering characteristics, a gel coat with UV inhibitors can be applied to the exterior of the panel at the time of manufacture.
FRP Panel Sizes:
Panel heights up to 10 feet and lengths up to 50 feet can typically be achieved. All fiberglass panels are custom made, cut and shipped to your individual specifications therefore minimizing waste for your specialapplication. Corrosion Resistant Fiberglass Panels can be manufactured in thicknesses from 1/8” to 1.25”.
Contact Fiber-Tech Today for Corrosion-Resistant FRP Applications
Corrosion-resistant fiber reinforced plastic (FRP) applications define the standard for safety-critical markets like chemical processing, air pollution control, mineral processing, water treatment and many more. Explore the limitless solutions Fiber-Tech can provide.
Call the “Composite Panel People”at Fiber-Tech Industries today!
Download Information Sheet for CORROSION RESISTANT Fiberglass Panels